By Cynthia Challener, CoatingsTech Contributing Writer
Powder coatings are widely used on many different metal substrates to provide durable, high-performance coatings with an attractive finish. With the development of powder coatings that cure at lower temperatures, this coating technology is making significant inroads in certain wood-based applications.
One of the biggest is medium-density fiberboard (MDF) used to produce home and office furniture, including desks, cabinets, shelves, and other products manufactured using flat-panel components. In these applications, powder coatings replace traditional laminates, providing greater flexibility, better performance, and more sustainable solutions.
MDF, which comprises particles of wood bonded with a synthetic resin, is particularly suited to powder coating. It is a readily available substrate that is highly consistent with a density profile and moisture content suitable for powder coating, according to Michael Knoblauch, president of Keyland Polymer, a developer, formulator and manufacturer of UV-curable powder coatings. Natural or solid wood species are more problematic to powder coat, he notes, due to their variable and unstable resin and moisture contents.
Access to powder coatings is also facilitating a trend in the office furniture market where MDF is widely used. End-users are moving away from traditional boxy looks to designs with more rounded corners and contoured edges, shapes that cannot be produced using lamination techniques.
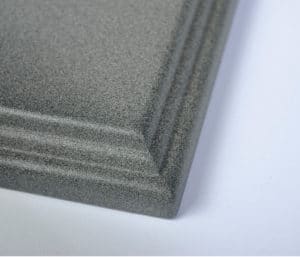
Photo Courtesy of Keyland Polymer
Using electrostatic attraction through the moisture in the MDF substrate, the powder coating is applied to the surface and then melted and cured with the application of heat in an infrared, convection, or hybrid oven (thermoset powder coatings) or melted with heat and then cured with UV light. In both cases, the coating resin bonds directly to the MDF fibers, leading to highly durable and attractive finishes.
“If a part can be designed and machined from MDF, it can be finished with a powder coating, because these coatings flow smoothly around curves, corners, edges, and cutouts,” Knoblauch explains.
Powder coating is a “disruptive technology” in these applications,” says J.T. Weis, CEO of Abcor Industries, a wood powder coater leveraging the latest thermoset infrared curing technology. The key reasons, he says, are the elimination of the requirement for edge banding (a common source of failure in laminates), reduction of the carbon footprint by as much as one-fifth compared to laminates, and a dramatic increase in design flexibility for design and product development teams.
“Powder coating on wood affords the ability to create both functional and design-focused components in a one-coat, single-step process,” adds Knoblauch.
Powder coatings are also solvent free, non-toxic, and contains no volatile organic compounds (VOCs) or hazardous air pollutants. Furthermore, powder coatings, Knoblauch says, maintain their original color, gloss, and texture even after frequent use and cleanings and do not experience the chipping, peeling, or delamination often observed with paint or laminate finishing options.
Most powder coatings used on wood substrates are based on epoxy, polyester, or epoxy-polyester hybrid resins, according to Weis. For coatings cured with heat, some require the use of curing agents while others are unsaturated and do not require such additives. Weis believes that thermal curing is essential to enable the crosslinking at the wood-fiber level necessary to achieve the desired level of durability.
“Powder-coated wood requires the right combination of flexibility and strength because unlike metal, wood substrates move,” Weis says. “That balance can only be achieved with deep thermoset curing. Most power coatings for office furniture are opaque, and it is difficult to get beyond a surface cure, which can lead to edge cracking when the furniture moves.”
Knoblauch offers a different view. UV curing, he says, provides instantaneous and certain cure when the lamp energy, dosage, and spectral output are matched with the cure chemistry in the UV-cured powder coating. In addition, because the MDF substrates are exposed to significantly less heat, there is less opportunity for degradation that can lead to cracking, outgassing, pin holing, and other defects.
Both agree that off-gassing of VOCs from MDF substrates is one of the biggest challenges when powder coating MDF. “For powder coating of wood, a quality film build is essential,” Weis explains. “Quality is negatively impacted when gasses are released into the melt state prior to curing and as crosslinking is beginning. Controlling off-gassing is therefore necessary to achieve control of the quality of the powder-coated product and thus ultimately the durability, flexibility, and strength of the finish.”
He notes that the key is to apply the right amount of energy during curing of the coating; too much will lead to unacceptable levels of off-gassing, while too little will lead to insufficient cure. Knoblauch adds that for UV-cured powder coatings on wood it is important to control the heat energy used to preheat the powder prior to application and then during melting prior to UV curing, which requires the proper balance of convection and IR heating.
Another challenge, Knoblauch notes, is controlling the application process to ensure that sufficient powder is applied on all surfaces being finished to realize the desired appearance and performance properties.
“In addition to quality,” adds Weis, “the thickness of the film is important to its performance. The right amount of powder must be applied to the substrate during every coating process with every substrate under all conditions. There is nothing more challenging than wood powder coating in the powder coating world.”
In all cases, using the highest grades of MDF and maintaining a proper level of humidity so the MDF has sufficient moisture–but not too much–to facilitate powder application and adhesion will also ensure more optimum results.
Advances in powder coating resin chemistry and application technology are helping to address the challenges of applying these coatings to MDF. The newer approach to getting the powder particles onto the MDF in use today leverages more electrostatic aspects, according to Weis. As a result, the behavior of the powder as it flows through the hose and out of the spray gun into the corona field is much improved.
“The atomization, particle-weight distribution, particle-size distribution, and other aspects of the powder structure effect how well a powder attracts to the MDF part and to what extent,” Weis says. “With this newer approach, the powder particle size is smaller and the size distribution narrower, which allows for greater uniformity and the production of what we describe as a pico finish. It isn’t a micro texture, but very flat visually and feels the same as a laminate and is attracting significant interest from our customers.”
For UV-cured wood powder coatings, a key advance has been improvements in the resins chemistry leading to increased coating durability, appearance, and curing results, according to Knoblauch. He also points to the development of UV LED lamp technology and powder formulations that can be cured using them. “UV LED curing required less energy and enables the UV powder coating of more complex geometries,” he explains.
Given the design, performance, environmental, productivity, and cost benefits of powder coating and continued advances in resin chemistries and application technologies specifically for powder coating of wood substrates, it is not surprising that powder-coated MDF products continue to take market share from laminates.
“The size of the wood powder market is growing exponentially, and if the technology and quality continue to improve, the market will continue on this exciting trajectory,” says Weis. Knoblauch predicts that within 10 years, wood powder coatings will be positioned as an essential finishing technology as companies continue to replace existing technology with this more productive, efficient, and environmentally friendly finishing technology.
Weis adds that if a low-temperature powder technology can be developed that provides a smooth, uniform coating without orange peel (a “piano-smooth” finish), growth of the market will be uncontrolled, because such a technology would meet the desires of design teams and customers for such a truly smooth finish that is more sustainable. Weis also notes the potential for wood powder coatings in exterior applications (outdoor furniture, decking, siding, fencing, garage doors, etc.) if the UV stability of existing formulations can be improved to meet the requirements of architectural standards.
CoatingsTech July 2021 | vol. 18, no. 7