By Cynthia Challener, CoatingsTech Contributing Writer
Waterborne coatings for industrial applications have been available for many years. Despite significant advances in resin technology, however, their use remains limited in these markets compared to their adoption in the architectural coating sector. This can be attributed to perceptions of poorer performance and higher costs when compared to solvent-based solutions. Expectations of OEMs and their customers are having some influence on the selection of waterborne coatings over solventborne options where performance and cost are comparable or more attractive. The biggest driver for switching to water-based systems is the introduction of stricter VOC and other regulations around the globe, which can be met via the use of waterborne coatings. (High-solids solventborne systems are another option). Improved performance of water-based industrial coatings, combined with advances in application equipment and technology, are also facilitating this shift.
Market Numbers
According to market research firm Markets and Markets, the global waterborne coatings market will grow at a compound annual growth rate of 5.05% from $58.78 billion in 2015 to $75.29 billion in 2020 (Figure 1). Water-based coatings have been widely used in the architectural segment for many years; it is increasing demand for waterborne systems in marine, coil, wood, metal packaging, printing inks, and electronics end-use industries that is expected to drive this significant growth, according to market research firm Grand View Research. Advances in resin and additive technologies to overcome flow, viscosity, foaming, and other performance issues are also creating opportunities for growth.
The largest regional market for waterborne coatings in 2014 was Europe, followed by Asia Pacific, which is growing at the fastest rate . . .
Acrylic resins are the most widely used resin type and are found in waterborne architectural and automotive refinish applications. Polyurethane dispersions (PUDs), according to Grand View Research, are experiencing the highest growth rate, particularly due to increasing demand in the coil coating and automotive sectors. Waterborne epoxies and polyvinyl chloride (PVC) coatings are also experiencing greater demand in electrical insulation, industrial finishes, automobile interiors, and office machine exteriors. The largest regional market for waterborne coatings in 2014 was Europe, followed by Asia Pacific, which is growing at the fastest rate, according to Grand View Research.
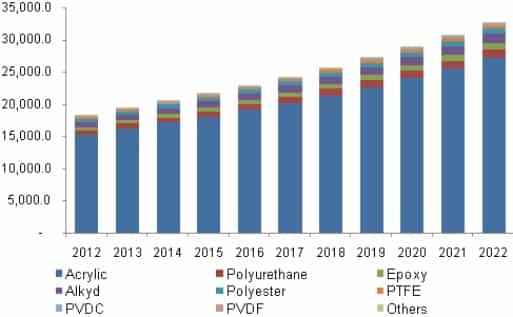
Figure 1—Global waterborne coatings market volume by resin, 2012-2022 (kilo tons). Source: Grand View Research
Solventborne Coatings Still Dominate in Industrial Applications
Compared to other coatings market segments, the industrial segment is one that tends to err more on the conservative side when it comes to new technology adoption, according to Mary Rose Correa, Industrial Acrylics marketing manager, North America at The Dow Chemical Company. “Often, the biggest challenge to coatings innovation in industrial applications lies in the fact that any new technologies developed are commercialized to replace incumbent technologies that have been used for decades,” she explains. In fact, the use of waterborne coatings is currently very low at less than 10% of the market, according to David Morton, group R&D director for Protective & Industrial Coatings with Hempel A/S. He notes that the perceived higher cost of waterborne inhibits the conversion of potential customers, especially in cases where there is a lack of regulatory legislation mandating the lowering of VOCs. This is particularly true in the United States, where options such as exempt solvents can be successfully leveraged to lower the VOCs of more “traditional” solvent-based chemistries at a lower cost and without the need for extensive equipment upgrades to apply and cure a waterborne option.
“Ease of use and wide application windows for solventborne systems are key drivers, especially for customers that are not equipped with process controls. And although regulatory requirements are a strong driver, solventborne technology has advanced such that high-solids/low-VOC solventborne coatings with desirable attributes are available to meet these regulatory requirements. This situation is especially true in markets where exempt solvents assist in meeting regulatory requirements and where customers have used abatement systems to meet requirements,” says Joanne Hardy, global R&D director for Axalta Coating Systems. “In addition, established practices and familiarity with the application of solvent-based materials means there can be a learning curve associated with the switch to water. Installed equipment may not be compatible with water, creating a need for capital improvements.”
. . . businesses are increasingly seeing the benefits of promoting themselves as sustainable companies and of having buildings that won’t be out of date if green building standards become stricter over time.
The general consensus is that regulations are the biggest driver of the adoption of waterborne industry coatings. “Although the regulatory environment in Europe demands the use of waterborne liquid coatings, solvent-based liquid coatings are still used about 90% of the time in the United States and Canada. There are exceptions in which U.S. and Canadian customers demand waterborne coatings for their low-VOC content, but regulatory requirements remain the dominant driver behind the use of waterborne coatings in industrial applications,” asserts Michael Kowalski, liquid product manager, Industrial Coatings with PPG Industries. Regulations can apply to large geographic regions (Europe, the United States) or sub-regions (California vs the Mid-West in the United States or United Kingdom vs Germany in Europe), according to Ginger Merritt, vice president, Coatings & Country Manager, China for Michelman. Currently the greatest changes are occurring in China, according to Anthony D. Woods, R&D director, Wood Coatings, AkzoNobel Performance Coatings.
There are some sectors, however, such as the automotive and furniture industries, where demand for more sustainable, waterborne coatings is coming from brand owners and OEMs, according to Merritt. “These companies are looking to establish an improved corporate image, because perception in the marketplace is important,” she observes. Woods comments, however, that consumer demand remains a minor driver in the industrial wood market. “Many furniture manufacturers struggle with how to communicate the concept of sustainability to consumers, and therefore, this driver tends to be more relevant for smaller, niche manufacturers,” he notes. Customers are becoming savvier, however, argues Katie Fagan, BASF marketing manager for Formulation Additives. “More often than not, it is a common goal with our customers to develop products and formulations that can have a significant impact on sustainability,” she says.
End-user demand for sustainable solutions for industrial coatings is increasing, agrees Robert Mussell, R&D director for Industrial Coatings with The Dow Chemical Company, but he does not believe it is a significant driver for change just yet. “End users like to talk about sustainability, but the demand for sustainability alone isn’t always enough to sway them to adopt waterborne coatings if they are costlier. If given the choice between solventborne and waterborne coatings with similar performance characteristics, customers may be slightly more inclined to convert, but higher rates of conversion would more likely happen if the performance was better or overall application cost was lower,” he states. Sustainability is more often an added benefit when other regulatory factors force a change to waterborne, but will likely not be the primary driver, Morton agrees.
In the flooring sector, for instance, there increasingly are expectations for flooring solutions tailored to overcome very sector-specific challenges. Examples include coatings able to withstand airplane hydraulic fluids in the aviation industry, floors that dissipate static electricity in the electronics market or bacteria killing finishes in the food and beverage sector, according to Ben Smith, vice president of Flowcrete Americas, a business of the Euclid Group. He does add, though, that the drive towards sustainability cannot be overlooked. “The more sustainable solution will always trump a similar but less environmentally friendly system, thanks to the fact that businesses are increasingly seeing the benefits of promoting themselves as sustainable companies and of having buildings that won’t be out of date if green building standards become stricter over time.”
Many Resin Chemistry Choices
A number of different polymer types are used to formulate water-based industrial coatings, and selection of the resin chemistry depends on the performance needs of each individual application. The versatility of the resin, whether the coating will be used indoors or outdoors, the type of substrate it will be applied to, the desired properties (hardness, flexibility, impact resistance, etc.), the application requirements and conditions (temperature, process control, substrate conditions, cleanliness, etc.), and the total cost of the solution are all factors influencing the choice of a specific waterborne industrial coating, according to Merritt.
Acrylic emulsions, PUDs, and epoxy polymers are most widely used and are chosen based on performance and cost, according to Hardy. Styrene acrylics should also be mentioned, as the trend is to move away from bisphenol A (BPA)-containing epoxy technology, according to Shiona Stewart, industry marketing manager for Transportation, Industrial, Furniture, and Floor Coatings with BASF. The adhesion, durability, and quick drying time of acrylates and PUDs, combined with the fact that these technologies can be used on different substrates, make them the resins of choice in many applications, adds Jon Cronin, sales director for Coatings, EMEA, with DSM Coating Resins. “Polyurethanes and epoxies are especially suited for heavy-duty protection needs in highly corrosive environments. They can help underlying substrates resist corrosion, withstand the elements often encountered in harsh environments, and the best systems can last for years to decades—an important quality considering the sizable investment required to protect infrastructure and equipment,” Correa asserts.
Cronin observes that waterborne alkyd dispersions were slower to be developed and introduced to the market, but have experienced increased demand in recent years due to the enhancement in application of their robustness, corrosion resistance, and drying performance. “Hybrids are another resin type seeing growing use,” says Cronin. “Urethane alkyd hybrids offer the best of both technologies, including mechanical toughness and even faster drying times.” Jeff Johnson, a research fellow with Axalta Costing Systems notes that polyesters are used less often due to issues with hydrolytic stability under alkaline conditions in waterborne formulations. Other less common waterborne industrial coatings include polyvinylidene fluoride (PVDF) and sol-gel coatings.
Waterborne 2K PU coatings are replacing solventborne 2K PUs in high performance exterior and higher-end furniture applications where scratch- and stain-resistance are required.
There are regional trends regarding resin preference as well. “In the United States and Canada, 1K (one-component) waterborne coating systems are primarily employed; most solvent-based coatings use two components (2K) to ensure proper curing. Europe uses more 2K waterborne coatings than the United States and Canada, but these coatings tend to require more complicated resins. There are 2K waterborne liquid coatings available in the United States and Canada, but their pot lives are generally poor; after mixing, applicators only have a half hour or slightly more to use them. Shops that use plural component mixing systems, in which mixing actually takes place in the spray gun, are generally best suited to use these types of coatings,” Kowalski explains. Morton notes, however, that more 1K waterborne chemistries are replacing traditional solvent-based alkyd and acrylic technologies for primers and topcoats because the impact of switching to water-based systems can be cost-minimized. He also points out that exempt solvents are typically a less-effective approach due to the amount required to meet regulatory standards in the market, and there is typically not a significant trade off with waterborne systems with respect to performance properties, application requirements, or curing times vs solvent- based options.
“On the other hand, waterborne coatings are less likely to be adopted for high-performance 2K applications such as urethanes and epoxies due to the availability of other chemistry options for lowering VOC content, including the use of reactive diluents, modest use of exempt solvents when allowed, and application modifications like paint heaters,” Morton says.
In the furniture sector, five key technologies are used, according to Woods. Multiphase, 1K film-forming acrylics combine toughness and flexibility for exterior joinery applications. 1K acrylics are also used for interior joinery/molding/doorskin applications, which are very cost-sensitive mass-market OEM applications. High-end acrylics and PU-modified acrylics/acrylic PUD blends give the appearance and toughness of a 2K PU in a 1K waterborne system for furniture and are experiencing growing demand in China. Waterborne 2K PU coatings are replacing solventborne 2K PUs in high performance exterior and higher-end furniture applications where scratch- and stain-resistance are required. Waterborne UV coatings are also a growing trend; these systems provide early handle-ability combined with scratch- and stain-resistance required for products that experience high use, such as office furniture and kitchen cabinets, according to Woods.
In the U.S. flooring market, cementitious urethane and more robust epoxy systems (25–30 mils) tend to dominate the industrial segment, according to Smith. “Despite a higher initial cost, cementitious urethanes are renowned for their durability and ability to create easy-to-maintain finishes that won’t incur expensive repairs or refurbishments,” he says. Fast-curing methyl methacrylate (MMA) systems are not as popular, potentially because they are trickier to install and have an off-putting odor, but Smith adds that the advantages of this type of floor are becoming more and more understood throughout the flooring industry. “Resin versatility is especially important in the flooring industry, particularly with respect to the ability to develop customized coatings with specific properties.” As an example, waterborne epoxy finishes can be made to dissipate static electricity before it can build up to problematic levels by incorporating a specially designed copper grid into the floor that safely grounds the whole floor area and avoids static discharges from occurring. “These coatings are important in the electronics sector, where static electricity build-up in the floor can damage sensitive components and equipment and even be a dangerous ignition source in areas with flammable gasses or substances on site,” Smith explains.
Challenges for Industrial Applications
“One of the biggest hurdles to increased adoption of waterborne coatings in industrial applications is that there needs to be a paradigm shift when it comes to viewing waterborne coatings as inferior to solventborne coatings. It is possible to achieve similar performance from current waterborne technologies that have specifically been developed to meet the demands of particular industrial applications, and Dow works to educate customers about these options that can serve their needs and offer added benefits including ease of use and an improved environmental profile,” Correa observes.
The main challenges to the use of water-based coatings in industrial applications, agrees Stewart, continue to be performance-related. Specific issues include corrosion resistance, weathering and UV degradation, and adhesion to a broad range of surfaces (e.g., steel, aluminum, plastics, composites). An additional challenge can be the overall sensitivity of applications performed in extreme environmental conditions, such as high humidity or low-temperature climates, she notes. Merritt comments that while there are plenty of examples where waterborne coatings are equal in performance to their solventborne counterparts, waterborne systems tend to be less forgiving with less-than-ideal application conditions. “Drying time is also a challenge because the evaporation of water requires much more energy than the evaporation of solvents (2260 J/g for water compared to 373 J/g for 2-butoxyethanol as an example), and application conditions are important. Drying is dependent on relative humidity and temperature, and is a challenging factor for all in-field applications. Additionally, film formation is dependent on temperature,” Merritt says. Other issues that need to be addressed, according to Merritt, include reducing the overall water sensitivity of the water-based coating films, which is due to the presence of residual surfactants, and their in-use cost.
Johnson asserts that the development of polymers that are stable in water and give coatings that are resistant to humidity exposure has been one of the advances that have improved the capability of waterborne coatings in various markets. Cost-in-use is not as easily overcome, however. The cost per volume of waterborne coatings compared to solventborne coatings is higher. In addition, the solids content of waterborne coatings is lower, thus more paint is required to achieve the right dry-film thickness, which can be time consuming and more expensive, according to Morton.
Application robustness is a concern for Kowalski. “Waterborne coatings show defects more easily, and it is easier for dirt to get into the system and cause defects. Solventborne coatings are more forgiving. The shelf-life of waterborne coatings in the can tends to be shorter as well—only six to 12 months—than solventborne products, which can last up to two years,” he remarks. Morton adds that a high level and standard of surface preparation/cleanliness must be adopted with waterborne coatings because if there is any oil contamination there will be wetting problems instantly. Another key challenge, according to Morton, is that changing from solvent- based coatings to waterborne coatings may require investment by the applicator because many industrial production lines are already set up for solvent-based coatings.
In automotive refinish applications, Kowalski points out that it is more difficult to achieve Class A automotive-type appearances with waterborne topcoats and clearcoats compared to solventborne systems. For industrial wood applications, the challenges are different for each segment, according to Woods. Preventing grain rise and the ability to achieve a high depth-of-image with clear grain structure and warmth in transparent coatings are issues for furniture and kitchen cabinetry applications, as is delivering adequate stain-resistance. “This hurdle is caused by the wood fibers swelling with water. Today this often means the first one or two coats are primarily alcohol-based stains and solution acrylics to seal the surface before waterborne sealers and topcoats can be applied,” Woods explains.
For building products, knot/tannin sealing remains an issue, while in wood flooring, the market has moved to UV systems that provide a good balance of productivity, regulatory compliance, and cost. In non-wood flooring applications, Smith notes that the perception still exists that solvent-based coatings perform better under duress than waterborne systems. “By looking at the compressive strength of a floor build-up, however, it can be ascertained whether or not a waterborne coating is up to the task at hand. Often when this is taken into account along with the advantages of having a seamless, impervious, colorful, customizable, and environmentally friendly surface, the full potential of waterborne coatings is comprehended,” he states.
Tackling the Issues
Issues with waterborne industrial coatings that continue to be addressed today include lower temperature cure, lower energy consumption, and increased productivity, according to Johnson. These attributes continue to drive the market as they lower cost for customers. To continue to advance coatings technology in these areas may require novel crosslinking chemistries and continued advances in resin synthesis, he adds. “Resin technology is a key contributor to the product performance and is one of the most valuable assets of a coatings company. While the fundamental building blocks of resin synthesis have not changed, advances in catalyst technology have created opportunities to create novel polymer architectures that have dramatically widened the range of coating performance available from water-based resins. Controlled polymer architecture also provides a means to reduce surfactant levels and to reduce the use of other water-soluble components used during polymer synthesis, resulting in improved application robustness through better spray atomization along with improved durability,” Johnson says.
“Innovation efforts in waterborne coatings continue to be focused on improvement of the robustness of waterborne applications,” notes Michelle D’Amico, liquid product manager, Industrial Coatings with PPG Industries. “Advances have been made in waterborne resin technology that address cure speed issues and help offset the limitations associated with the need to evaporate water prior to curing, which is greatly affected by temperature and humidity,” she notes. Currently, PPG is researching ways to make waterborne coatings more user friendly and is reformulating many of its older products to make them easier to apply. Michelman is in the process of developing new anti-blocking acrylic polymers for wood, according to Merritt. She adds that advances in waterborne resin technology have helped overcome challenges such as wetting and surface penetration on wood and concrete, and due to the naturally low viscosity of water-based systems, their self-levelling performance in flooring applications allows for the use of polymers with higher molecular masses that impart resistance to chemical attack and exhibit stronger mechanical properties.
BASF is focusing on increasing productivity. “Anything that reduces down-time for plants during initial coating or maintenance re-coating is important. Improving cure time, application time, spray application ability, and making coatings easy-to-clean all help reduce that down-time, which is a cost benefit to the plant on multiple fronts. And all these end-benefits typically require a smart resin and smart additives, especially in waterborne coatings,” notes Fagan. “We are targeting development of water-based chemistries that provide labor and cost saving benefits due to the reduction of the number of coats applied to a substrate, as well as higher-performance chemistries that will enable formulators to access heavy-duty industrial environments with waterborne technology,” Stewart comments.
. . . advances in catalyst technology have created opportunities to create novel polymer architectures that have dramatically widened the range of coating performance available from water-based resins.
Many advances in resin technology are occurring through collaborations across the supply chain, according to Cronin. “We are participating in an increased level of co-development projects with our customers. As a result, we are no longer only a resin supplier, but an extension of the R&D groups of our customers. We believe that being an innovation partner leads to the most fruitful outcomes,” he states. DSM has also observed an increases emphasis on looking further down the value chain for regulatory and macro-economic issues that connect all the way back to resin suppliers, according to Cronin. “For example, we have a global product stewardship task force that monitors possible potential pressures. This early warning system helps our customers take necessary actions in a timely manner,” Cronin observes.
For industrial wood applications, the demand for waterborne UV solutions is increasing across all regions with clear inroads being made in the kitchen cabinet segment.
Sustainability is also an issue that must be addressed across the board, throughout production, transportation, installation, maintenance, and even at the end of a floor’s lifecycle, according to Smith. “The need was clearly demonstrated with the issuance of the latest version of LEED, which has an increased focus on indoor environmental air quality and the impact that several categories of materials, including flooring, have on it. “Waterborne resin systems are now a much more attractive prospect because they exhibit much less outgassing behavior, are unlikely to dust, and are made without the VOCs, nonyl phenols, solvents, and other potentially harmful ingredients found in many other flooring materials,” he says.
For industrial wood applications, the demand for waterborne UV solutions is increasing across all regions with clear inroads being made in the kitchen cabinet segment, where its improved productivity can help customers expand while staying within their VOC air permits, according to Woods. He notes, however, that the technology is limited to auto-spray applications due to the health, safety, and environmental issues associated with hand-spraying of low-molecular-weight oligomers, which means such solutions are only really accessible to OEM producers prepared to make line investments.
Looking at the Longer Term
“The stakes are high to ensure industrial coatings perform and meet the required specifications, so it is understandable why infrastructure owners, for example, would be wary of specifying new coatings into their industrial projects. That being said, when new technologies are actively being used in the market, customers then have concrete examples that they can review to learn about a technology’s performance ability. Once formulators and brand owners see that a solution is available that is more sustainable and performs as well, they may be more open to change. The key here is to continue to make strides in the development of waterborne alternatives so we as an industry can continue to make inroads and increase adoption of sustainable solutions across all coatings segments,” states Mussell.
Continued advances in resin technology are key to next-generation coatings technology, asserts Johnson. “Single polymer solutions no longer deliver the properties needed in advanced coatings; coating systems today are required to deliver multiple layers of performance. Bringing multiple components into one system and optimizing these complex systems to deliver application and physical properties for the customer and end consumer has changed the way coating formulators approach problems. Hybrid chemistries and multi-component systems are already the norm and will expand. The growth in modeling and simulation tools also enables a broader range of experimentation and development and will accelerate advances in coatings,” he adds.
As a firm believer in making coatings as sustainable as possible, DSM sees biobased resins as key to the future of the coatings industry and industrial coatings. “Biobased resins under development today do not require a sacrifice in performance,” observes Cronin. “In addition, they are more sustainable with a reduced carbon footprint, go beyond the current regulations, and tackle the issue of decreasing fossil-fuel stocks.”
Changes in China are also important to the future of waterborne industrial coatings, according to Mussell. “While this region may have been behind North America and Europe in the initial conversion from solventborne to waterborne options, China is definitely picking up the pace in converting to waterborne options and actually working to go beyond the regulations.” He notes that it will be interesting to see how the conversion develops in China, since it has been moving much more rapidly than conversion rates in North America and Europe over the past several years. Morton adds that China will be a noteworthy test bed on how the industry handles tighter restrictions. “We believe that further tightening of restrictions on VOCs and other similar legislation will lead to significant developments in the industry, particularly on the processing side,” he remarks. As the use of waterborne formulations becomes more prevalent in other regions around the world, PPG is committed to developing technologically advanced products to meet the evolving needs of its global customers, according to D’Amico. “We are currently investing in waterborne technology research of a full layering system that incorporates a primer and compatible topcoat. By working on development projects while considering all layers of the application, PPG can use layer synergy and tailor each product line to meet the full performance requirements of the system,” she explains.
CoatingsTech | Vol. 14, No. 10 | October 2017