One of the key drivers in the development of new coating technologies today is the need to increase the sustainability of both coating formulations and their application processes. Leading solutions include high-solids solventborne systems, water-based coatings, and formulations that cure when exposed to ultraviolet (UV) or electron beam radiation. All of these options offer reduced volatile organic compound (VOC) emissions, but each has its own advantages and limitations in different applications, which range from printing ink / graphic arts and wood finishes to automotive, aerospace, and industrial metal protection.
For pipe and tubing, Allied Photochemical reports on two case studies that highlight the advantages of UV-cured over water-based systems. “In today’s competitive manufacturing environment, it is necessary to drive process efficiencies, improve sustainability, and deliver a high return on investment (ROI) for stakeholders while also manufacturing a superior product,” says Michael Kelly, chief customer officer at PhotoChemical. “UV coatings deliver on all four points,” he asserts. It is, therefore, essential for applications where UV curing is practical to consider the advantages that this technology may provide, according to Kelly. “In pipe and tube applications, for instance, UV coatings technology offers a unique opportunity for users to dramatically improve their manufacturing processes and sustainability footprints and deliver real ROI in the form of less coating cost per linear foot of pipe or tube,” he explains.
In pipe and tube applications, for instance, UV coatings technology offers a unique opportunity for users to dramatically improve their manufacturing processes and sustainability footprints and deliver real ROI in the form of less coating cost per linear foot of pipe or tube.
One of the perceived concerns regarding adoption of UV curing technology is that it has both higher upfront investment and ongoing operating costs and thus higher overall product costs. In two customer case examples in which each customer had to choose between investing in an upgrade to an existing water-based coating system or a new UV coating system, Allied Photochemical was able to show that this perception is faulty. The examples included coating of OCTG (Oil Country Tubular Goods) / line pipe and mechanical tube products, and for both, it was found based on quotations from various partner companies that the overall capital costs for waterborne and UV-curing systems were comparable, according to Kelly. “The main difference was the heating system used for each: induction heating and microwave / UV lights, respectively. While both have similar capital investment costs, they have very different operating costs and uptime costs,” he observes.
For the OCTG / line pipe example, the customer was looking to increase the line speed of the coating application process, improve corrosion resistance and reduce end-user complaints, and eliminate wasted floor space due to the need for drying tables. The existing water-based coating (18.5% solids) cost $11.89/gal and covered 296.7 ft2 at a 1.0 mil DFT (Dry Film Thickness). This product was proposed to be replaced with a 100% solids UV-cured coating priced at $39.70/gal but offered coverage at 1.0 mil DFT of 1,604 ft2. Using a proprietary functional pipe coating model, Allied Photochemical estimated the cost per linear foot for the existing water-based coating and the proposed UV coating solution for OCTG / line pipe with a diameter of 9.625 in. applied at thickness of 1.0 mil. According to the model, for a 2,000,000 million linear foot run, switching to the UV coating would afford cost savings of $77,197.74 ($771,977.36 at 20,000,000 million linear feet).
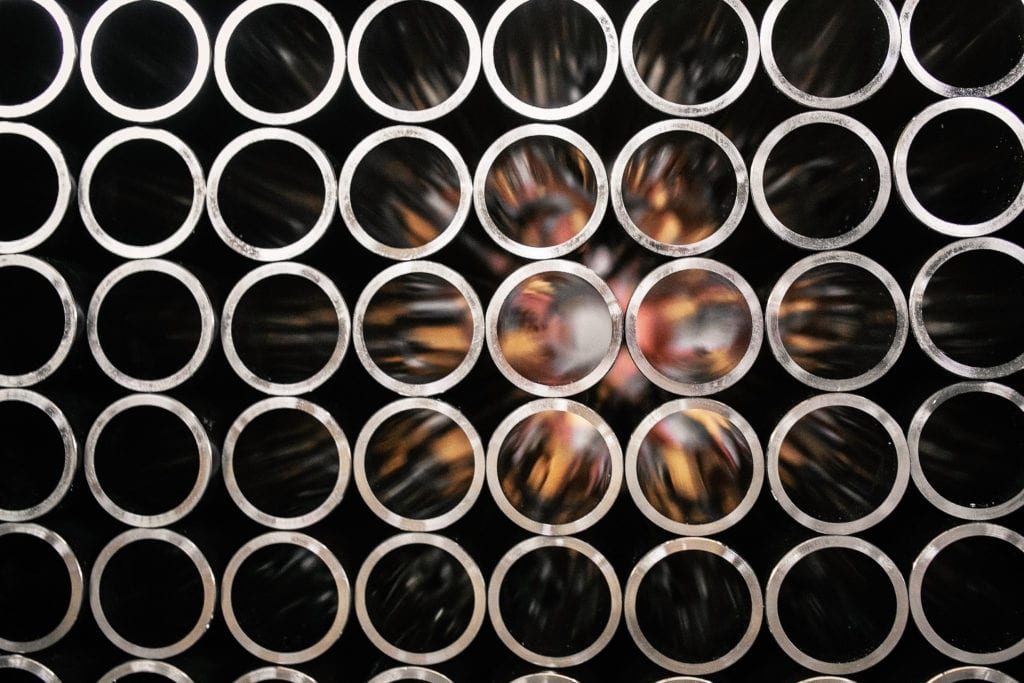
[The UV coating] also outperformed the waterborne coating in humidity, adhesion, and UV resistance testing.
In the case of the mechanical tube, the customer wanted to improve the corrosion resistance and aesthetic appearance of the coated tubes in order to reduce end-user complaints, increase the line speed, minimize humidity and temperature impacts on the coating process, and eliminate VOCs and HAPs. Although a water-based coating was used at the time, it contained ~11% of a flammable cosolvent. At $19.79/gal, this coating comprised 30.5% solids by volume and covered 489.2 ft2 at 1 mil DFT. The proposed 100% solids UV coating alternative priced at $59.25/gal but offered coverage at 1.0 mil DFT of 1,604 ft2. “Once again,” says Kelly “the performance of the UV coating exceeded that of the water-based system and met all of the higher target specifications established by the customer. The line speed was increased from 175 fpm to over 275 fpm and ~70% less coating had to be manipulated. In addition, handling/exposure of the flammable water-based system was eliminated.” The other process advantages outlined for the first example were also realized, he adds. In this case, the cost analysis using the functional pipe coating model (2.0-in. diameter tube coated at a thickness of 0.3 mil) predicted savings of $2,759.29 for a 5,000,000 million linear-foot run and $27,592.94 for a 50,000,000 million linear-foot run. Based on all of these results, the customer elected to implement a new UV coating system.
“In both examples, UV coatings allowed the customer to run much faster, with a smaller physical footprint, lower WIP, and reduced quality and energy costs, resulting in a much cleaner, green, sustainable process while delivering an improved ROI to the bottom line,” Kelly concludes.
CoatingsTech | Vol. 17, No. 8 | August 2020