By Adalbert Huber and Frank Maile, Schlenk Metallic Pigments GmbH
Introduction
Aluminum-based effect pigments are widely used in automotive coatings, but it has been found that such coatings frequently disturb the transmission of radar signals, if the radar source is hidden behind the coating. To measure this reduction in transmission, the permittivity dielectric constant (e) and the loss tangent, tan (d) (dissipation factor) of radio waves in the desired frequency band are used. Many published results show that the e increases with rising pigment mass concentration,2 while d changes are negligible. Figure 1 shows frequently cited data where the relative permittivity of automotive effect coating (including metal-based effect pigments) is analyzed with respect to the metal mass content.1,3 According to Pfeiffer, the exemplary limits of radar transmission in terms of relative permittivity of automotive coatings are assumed to be < 10 as uncritical, < 30 as little critical, < 50 as medium critical, and > 50 as highly critical.3
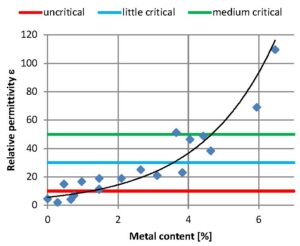
Figure 1. Permittivity vs. metal content of automotive coatings together
with typical limits of applicability for radar sensors.3
With a lack of information on the various properties of effect pigments used in the experiments (e.g., particle size distributions, thickness distributions, densities), no other conclusions were drawn other than to avoid or minimize the metal-containing effect pigments.4-7 The requirements would imply a lot of effort to reformulate coatings components, and many of the appearance targets such as hiding, flop, lightness, and chromaticity, as well as suitable LIDAR visibility,8 would not be fully reached.1 Therefore, the present article deals with the radar transmission behavior of well-defined, metal-based effect pigments in combination with the expected coloristic requirements. There is a special focus on Metal Interference Pigments (MIP), introduced to the market under product names as Paliocrom, Meoxal, and Zenexo.
Experimental
Base coatings containing well-characterized, metal-based effect pigments were prepared with different pigment mass concentrations (PMCs) by a pneumatic spray application, at a layer thickness (T ) of 14 μm on an optical transparent, 2-mm thick sheet of polycarbonate. No filler and no clear coat were used. The transmission of those samples is measured with a Radome Measurement System2 at a frequency of 76.5 GHz for a perpendicular incidence. The substrate (the polycarbonate sheet), without the base coat, exhibits an e of 2.736 and tan (d) of 0.007.
The LIDAR reflection measurement was performed at a wavelength of 905 nm, utilizing an Ulbricht Sphere with a measurement geometry that excluded the specular component. This configuration ensured that only the integrated, diffusely scattered IR-radiation was detected. It was hypothesized that a high level of diffuse LIDAR reflection could serve as a relative measure for ensuring good LIDAR visibility.
Applying the same coating, as used for the radar measurement, on black and white steel substrates and adding a 40 μm clear coat on top, the coloristic data were evaluated using a goniophotospectrometer BYK-mac i. Thus, the color values for geometries of aspecular angles of -15°, 15°, 25°, 45°, 75°, and 110° for a light incidence of 45° were measured.
The effect pigments are characterized by measuring the densities using an Ultrapyc 1200e instrument, the equivalent diameter distributions by a Sympatec Helios/Quixel instrument, and the thickness distribution by Scanning Electron Microscopy.
Continue reading in the September-October 2023 digital issue of CoatingsTech.