By Yuting Li, Shi Yang, and Scott Cooley, Polynt Composites USA, Inc.
Vegetable oil modified urethane (OMU) has been widely used in wood flooring applications for many decades. Due to tightening volatile organic compound (VOC) regulations in recent years, the market has been slowly shifting towards waterborne systems. However, most of the current waterborne OMUs either still contain N-Methyl-2-pyrrolidone (NMP), or the VOC is still relatively high at 135–250 g/L, while the nonvolatile (NV) content is relatively low at 32–38% and thus requires multiple coats to achieve performance properties.1 This article demonstrates a recent breakthrough in the development of a novel NMP-free waterborne OMU with a VOC <100 g/L and a high 45% NV content that maintains the exceptional performance properties of traditional solventborne and waterborne OMUs in the market. Its potential applications include but are not limited to high performance clear wood floor coatings, conformal coatings, air dry, and force cure coatings.
Introduction
Conventional solventborne vegetable oil modified urethanes (OMUs) have been a mainstay in wood flooring and clear varnish applications for many decades.2 Since their introduction into the United States in the early 1950s, their usage has grown steadily. They are typically supplied as a one package system, and once fully cured in the presence of metal drier, they can form a densely crosslinked thermoset polymer film. OMUs find application in the toughest environments, including gymnasium and athletic floors, as well as clear varnishes for hardwood floors in homes, offices, and other public buildings. While favored by the professional flooring contractor, they are also used by the do-it-yourself (DIY) homeowner, for everything from floors to cabinet refinishing to wood furniture restoration.
In these coating systems, the volatile organic compound (VOC) levels are typically in the range of 450–550 g/L. However, due to tightening VOC regulations in recent years, these high VOC solventborne OMUs are facing significant challenges. One common approach to develop low-VOC solventborne OMU is to reduce the amount of solvent to make a high-solids-content varnish. Because the viscosity of the polymer solution is directly proportional to its molecular weight (MW), this high-solids-content varnish must have a lower molecular weight to maintain a workable application viscosity. However, this lower molecular weight varnish shows poor film performance such as slow dry and soft film.
Another approach to develop low-VOC solventborne OMU is to use exempt solvent to replace all or part of the solvent used in the resin system. Typical exempt solvents include but are not limited to p-chlorobenzotrifluoride (PCBTF) and volatile methylsiloxane (VMS) due to their suitable flash point and evaporation rate. In this approach, the polymer molecular weight can be kept close to conventional solventborne OMU, thus the film performance is not sacrificed too much. Possible disadvantages for this approach include compatibility between the solvent, odor, and sometimes film lapping. Both approaches have been used to develop low-VOC (350 g/L) OMU varnishes. Recently, a 275 g/L VOC solventborne OMU varnish with reasonable dry time and film hardness3 was successfully developed. However, it will be quite challenging to push the VOC even lower to a level less than 200 g/L. Further development of waterborne systems may be the only solution for achieving this extremely low VOC.1
Waterborne polyurethane dispersions (PUDs) are one of the fastest growing segments for the surface coating industry due to technological advances that have made them effective substitutes for their solvent-based analogs. Conventional PUD is prepared by several routes, and the polymer formed is a predominantly linear polyurethane-urea. The polyurethane-urea dispersion forms a film by lacquer dry, which is by evaporation of a cosolvent, water, and neutralizer to form a thermoplastic film. Several crosslinking methods are available to post-crosslink the film into a thermosetting polymer, thus the film performance can be increased further. Because PUDs have lower amounts of VOCs and hazardous air pollutants (HAPS), they are used in many industrial and commercial applications where their ease of use and performance properties rival that of their solvent-based analogs. PUDs are formulated as air dried or baked coatings for flexible and rigid substrates such as leather, fabric, plastics, paper, and wood.
Fatty acid-based vegetable oil can also be incorporated into a waterborne PUD system; such system is normally called a waterborne OMU. Due to the presence of an unsaturated fatty acid segment, it can be formulated into a varnish by adding metal drier. After applying this high molecular weight urethane as a coating, it initially forms a hard lacquer dry film, followed by autooxidation to form a crosslinked film. Similar to conventional PUD, the viscosity of this dispersion is less dependent on molecular weight than its solvent-based counterparts. Therefore, such waterborne OMU overcomes the slow dry and soft film issues commonly seen in lower VOC solventborne systems. In addition, the “post-crosslinking” reaction resulting from the oxidative cure of the fatty acid segment that happens during or after film formation imparts the film with good mar resistance and black heel mark resistance similar to that of a solventborne OMU. The high molecular weight polymer and urethane linkage not only improves hydrolytic stability,2 but it also improves abrasion resistance, which is important for hardwood floor finishing applications.
Similar to conventional PUDs, most waterborne OMUs contain NMP as a cosolvent. The cosolvent in PUD aids in the synthesis process and in film formation. Recently, due to tightening regulations and health safety concerns, NMP has become a major issue in many applications and, therefore, NMP-free PUD development has become increasingly important. Several NMP replacement solvents have been used to make NMP-free PUD, including N-ethyl-2-pyrrolidone (NEP), N-butyl-2-pyrrolidone (NBP), and dipropylene glycol dimethyl ether (DMM). However, both NEP and NBP have a chemical structure similar to NMP; all belong to the same cyclic amide catalogue. The acetone stripping process can also be used to make solvent-free PUD, but this process is time consuming and quite expensive. Another drawback for waterborne OMU compared to solventborne OMU is lower solids content, which affects film build. Table 1 lists the resin properties of several commercially available waterborne OMU resins.
This article demonstrates a recent breakthrough in the development of a novel NMP-free fourth generation waterborne OMU with a VOC <100 g/L and a high 45% NV content that maintains the exceptional performance properties of traditional solventborne and waterborne OMUs in the market.
Discussion
This new and unique resin is synthesized via the typical PUD synthesis process: a prepolymer is first synthesized by reacting fatty acid based intermediate and dimethylolpropionic acid with aliphatic isocyanate in the reactor; the prepolymer is then dispersed into water after neutralizing with tertiary amine, followed by chain extension with polyamine. The nonvolatile content of the resin is 45+/–1%, similar to 3rd Generation WB OMU III, and both have the highest currently available NV in the market. In contrast with 3rd Generation WB OMU III, this new resin is NMP-free and complies with many of the latest regulations.
Similar to conventional solventborne OMU, a drier is needed to facilitate the oxidative drying process, as shown in Figure 1. Typical driers include but are not limited to iron, cobalt (Co), and Manganese (Mn). Iron drier is preferred because it is supplied in water and can be added into the resin system directly under mild mixing conditions. A concentration level of 7.5 ppm iron on resin solids is sufficient to facilitate the drying process. Though Mn- and Co-based driers can be used, most are supplied in organic solvent, and the ion concentrations are normally very high compared to Iron-based driers. Therefore, special care must be taken to avoid gelled particle formation during the drier addition process. To ensure optimum film performance, it is recommended to allow the drier to sweat into the resin system for at least seven days before application.
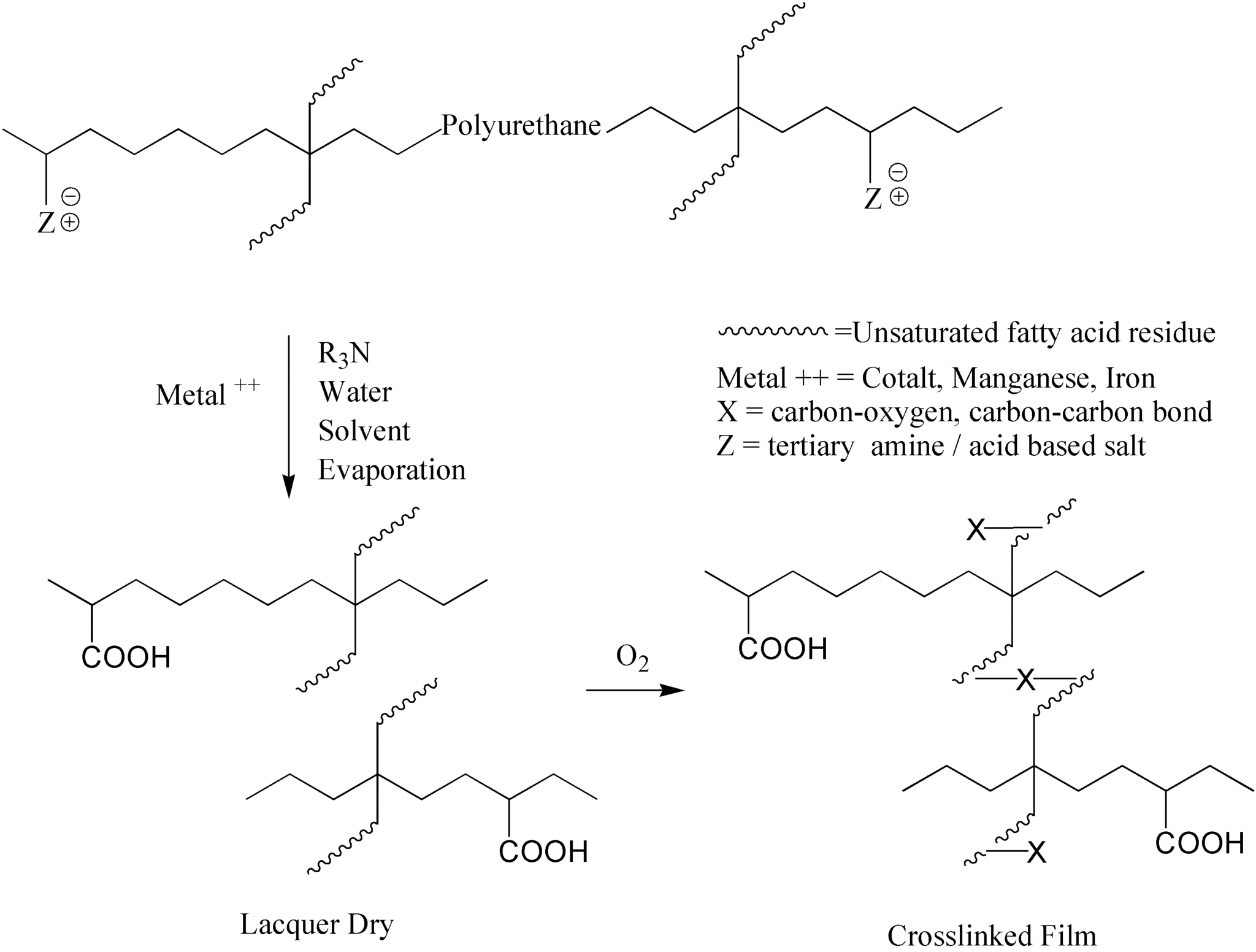
FIGURE 1—Waterborne OMU drying process.
Once the drier is added, no other additive is needed for film application, though for best film formation, a surfactant may be added to address bubbles or craters in the film. In contrast to other waterborne OMU products, this resin does not contribute to significant foaming during the application process. However, if needed, the addition of 0.05% VOC-free silicone defoamer into a clear varnish formulation has been found to be effective for crater-free films.
The Brookfield viscosity of this new resin is in the range of 200–1800 cps. Though the varnish can be applied for film performance testing after drier addition, the varnish viscosity is still very high and, therefore, a dilution with water may be needed to achieve practical application viscosity. As can be seen in Figure 2, cutting to an NV between 40–43% with water can lead to a workable application viscosity from 60–170 cps. Cosolvent such as dipropylene glycol monomethyl ether (DPM) and tripropylene glycol mono methyl ether (TPM) can also be post added into the resin system. The system viscosity will drop initially, but may start to increase as more cosolvent is added, mainly due to the swelling of the particles caused by the additional cosolvent. Post adding more cosolvent can also increase the resin film performance as is further discussed below.
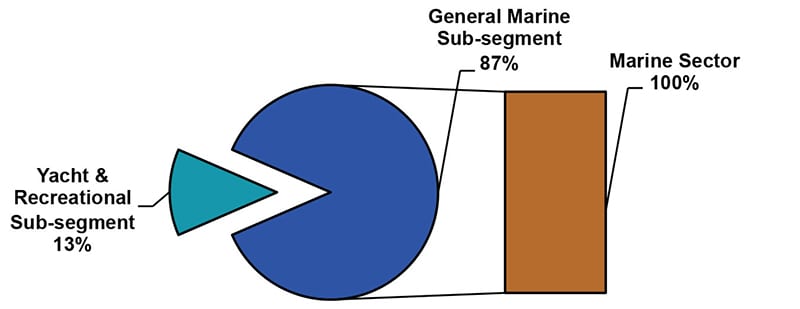
FIGURE 2—Novel waterborne OMU dilution curve with water and cosolvent.
Dry Time
In the lower VOC solventborne OMU system, dry time is a major concern due to the lower molecular weight of the polymer, and extensive oxidative cure must be realized before the film is dry to touch. The waterborne OMU counterpart normally dries very fast since the polymer has a very high molecular weight, and the drying process is simply the evaporation of cosolvent and water. As can be seen in Table 2, varnish based on this new resin can form a tack-free, amber color film in just 15 min compared to 40–75 min as seen with other commercial waterborne products. The special design of the resin composition is advantageous for applications that require fast dry. However, the dry time can be slowed down by adding more cosolvent such as TPM and propylene glycol (PG). For example, with PG as cosolvent, the dry time can be increased to 47 min when the VOC level is increased to 186 g/L.
Gloss
The new resin is capable of forming a very high gloss film, as shown in Figure 3. Similar to other commercial waterborne OMUs, the 60° gloss can easily reach 90, while the 20° gloss can reach 80. It also has good response to flatting agents like untreated fumed silica when lower gloss films are desired. As shown in Figure 4, 4% untreated fumed silica on resin solids can successfully yield a matte finish.
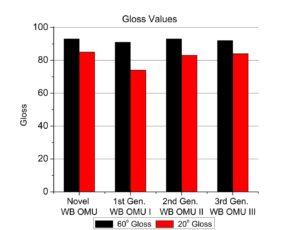
FIGURE 3—Gloss of novel waterborne OMU vs commercially available waterborne OMUs.
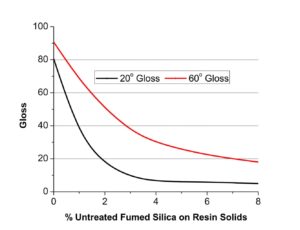
FIGURE 4—Novel waterborne OMU gloss vs level of untreated fumed silica flatting agent.
Hardness
As recommended by the Maple Flooring Manufacturers Association (MFMA), a Sward rocker tester (ASTM D2134) is used to compare the film hardness of the new resin and other commercially available waterborne OMUs. In general, most of them show similar Sward hardness values. Also a measure of surface cure, Konig hardness evaluates hardness of a coating by measuring the time taken for the amplitude of a pendulum’s oscillation to decrease from 6° to 3°. In the case of Sward and Konig results, hardness development was measured at one and seven days, and results are exhibited in Table 3.
Both the new resin and the other commercial waterborne OMUs show a similar pencil hardness of HB after a seven-day cure.
Rheology Profile
A very high NV (>40%) varnish with reasonable working viscosity can be formulated based on this new resin, thus only two coats are needed to achieve the desired film thickness that typically requires three coats with conventional medium NV (30%) varnishes. Some formulators may also find it useful in formulating medium NV varnishes, and in this case, because the varnish viscosity is very low, a thickener may be needed to increase the varnish viscosity. Shown in Figure 5 are the viscosity changes vs the level of polyurethane-based associative thickener added to the varnish. A level of 0.25% on resin solids is enough to boost the viscosity from 60 cps to 670 cps.
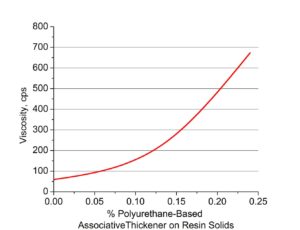
FIGURE 5—Viscosity of novel waterborne OMU vs level of polyurethane-based associative thickener.
Mar Resistance
Similar to solventborne OMUs, which have excellent mar resistance due to the oxidative cure from the unsaturated fatty acid segment, all of our early generation waterborne OMUs have excellent mar resistance properties without the addition of waxes. For this novel WB OMU, mar resistance can be achieved as soon as two days after film formation; excellent mar resistance can be fully achieved in seven days.
Chemical Resistance
ASTM International has test methods for the chemical resistance of coatings, and typically ASTM D1308 test method is used. These tests are based on placing specified chemicals on a horizontal finished part and covering with a watch glass. In this study, a total of 26 commonly available chemicals were evaluated and rated after an exposure time of four hours. The finish should not be damaged or discolored. A rating of 5 means no effect, while a rating of 0 means the film has been totally destroyed. As can be seen in Table 4, the new film exhibits excellent chemical resistance towards most common chemicals with an average rating of 3.88; similar to commercially available waterborne OMUs.
Cosolvent is not required for this product, but if it is desired, solvents such as DPM or TPM may be added directly under agitation. Increasing the VOC to 130 g/L has been shown to improve properties such as mar and chemical resistance.
Solvent Resistance
Solvent resistance was evaluated using ASTM D5402. Testing involves rubbing the surface of a film with cheesecloth soaked with selected solvents until failure or breakthrough of the film occurs. Similar to other commercial waterborne OMUs, this new resin can also resist more than 200 methyl ethyl ketone (MEK) double rubs, indicating the excellent solvent resistance resulting from post crosslinking (Table 5).
Flexibility
Flexibility tests are used to evaluate a coating’s ability to resist cracking. Impact resistance is a good test for assessing a coating’s capacity to avoid cracking and peeling from the substrate when it is exposed to a falling weight, which causes a deformation. This is especially important in applications related to the flooring industry where falling objects are common. Using ASTM D2794, results indicate that the new resin can pass 160/160 in./lb for both direct and reverse impact. Bend tests, such as the conical mandrel test, give indication to the elongation of the coating and its adhesive strengths when exposed to bending stresses. This new resin can also pass 1/8 in. conical mandrel bend test. Both methods of testing indicate that this film has excellent flexibility.
Abrasion Resistance
A good coating should offer protection against abrasion and scratches. One of the most common tests for the evaluation of abrasion resistance is by using a Taber Abraser (ASTM D4060-14). Figure 6 presents Taber Abraser test results reported as the wear index of the coating; the weight loss for the amount of revolutions made under a specified load of 1000 grams using a CS-17 stone. It is apparent that the new resin exhibits abrasion resistance properties comparable to three commercially available waterborne OMUs and better than a 450 g/L solventborne system.
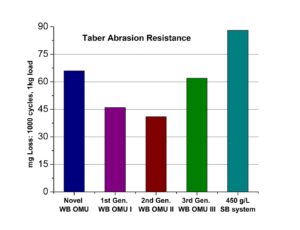
FIGURE 6—Abrasion resistance of novel waterborne OMU vs commercially available OMUs.
Conclusion
A novel NMP-free waterborne OMU with a VOC <100 g/L and a high 45% NV content that maintains the exceptional performance properties of traditional solventborne and waterborne OMUs in the market has been successfully developed and scaled up for commercial sale. With fast dry, high gloss, excellent mar resistance, chemical resistance, solvent resistance, good adhesion over acrylic sealer, and good storage stability, its potential applications include but are not limited to high performance clear wood floor coatings, conformal coatings, air dry, and force cure coatings.
References
- Yang, S., Cooley, S., and Albrecht, A., “Vegetable Oil-Based Urethanes for Wood Coatings,” PCI Magazine (October 2017).
- Petschke, G., “Waterborne Oil Modified Urethane for Compliant Wood Floor Varnishes,” Western Coatings Societies, 22nd Biennial Symposium, 1995.
- Hayes, K., “275g/L VOC Compliant Solvent-borne Oil Modified Urethane,” Western Coatings Societies 33rd Biennial Symposium, 2017.
This article was presented at the American Coatings CONFERENCE, April 9–11, in Indianapolis, IN.
CoatingsTech | Vol. 15, No. 6 | June 2018