By Leo Procopio, Paintology Coatings Research LLC
The 2023 CoatingsTech Conference, organized by the American Coatings Association, convened June 26–28 in Cleveland. Exploring the theme “Coatings Technologies: Adaptation in a Complex World,” the first two days included several short courses, keynote and plenary addresses, the Mattiello Award Lecture, student posters, and more than 30 technical presentations on coatings technology. Although all the presentations cannot be summarized here, this article highlights several of the addresses and technical presentations.
The keynote presentation by Dr. John Gilbert, chief R&D officer of Behr, kicked off the first day of technical sessions. His lecture, “Developing Coatings for a More Sustainable Future,” discussed the role of sustainability in the coatings industry and strategies for more efficient use of coatings.
On the second day of the conference, Dr. Kurt Wood, industry consultant and retired senior principal scientist at Arkema, was awarded the Joseph J. Mattiello Lecture Award, which honors an individual who has made outstanding contributions to science, technology, or engineering related to the coatings industry. Wood’s lecture, titled “Visualizing How Coatings ‘Fail’–Service Life Viewed through the Lenses of Coatings Science,” focused on factors affecting the weathering of coatings and their service life.
Day 2’s busy agenda also included a panel discussion on the “Future of Laboratory Work,” where several industry experts discussed the role of digitalization, automation, machine learning, artificial intelligence, and data security. Following the panel discussion, Dr. Victoria Scarborough of The ChemQuest Group delivered the plenary address, “A Heat Map of New Technology in a Post-Pandemic World,” an examination of megatrends that are driving technology and offering opportunities for the coatings industry.
The final day of the conference focused on environmental, health, and safety issues facing the coatings industry, as experts from government and ACA addressed developments that impact business and compliance efforts. As the conference drew to a close, Dr. Dane R. Jones, professor and associate dean, emeritus, at California Polytechnic State University, was presented the inaugural David F. Darling Prize. This award, named for the late ACA vice president of health, safety, and environmental affairs who passed away in 2022, honors Darling’s legacy in the industry.
For 25 years, Darling served as a staunch advocate for the coatings industry, extending his expertise and contributions into the areas of sustainability and product stewardship, where he developed a wide network of professionals with the goal of creating science-driven solutions for the coatings industry. Demonstrating that same commitment and focus, Jones was recognized for his research that has played a key role in the quantification, rationalization, and realization of air pollution reduction efforts, and have provided valuable tools for industry’s continuing commitment to create a more sustainable future.
Furthering the discussions of industry advances, the conference presentations covered new research and technologies designed to address some of the issues facing the paint and coatings industry today, and this article spotlights a selection of the addresses and technical talks. As always, readers are encouraged to seek out papers, authors, and presenters for more information, as well as check future issues of CoatingsTech magazine for the publication of some of the papers presented at the 2023 CoatingsTech Conference.
Sustainability
Sustainability is something the paint and coatings industry has been concerned with for decades. Often, regulations have been the impetus for efforts toward sustainability. These efforts, such as removing volatile organic compounds (VOC) content or materials of concern from raw materials and coating formulations, have also resulted in the development of safer products. Now the sustainability journey also encompasses ideas such as using more renewable or biobased materials, increasing coating durability to lower lifecycle costs, and improving production processes to lower carbon content or even achieve carbon neutrality, among others. It is heartening to see that our industry has truly embraced the underlying importance of working toward a more sustainable world, and many of the presentations at the CoatingsTech Conference clearly demonstrated that commitment.
For instance, John Gilbert’s keynote presentation—”Developing Coatings for a New Sustainable Future”—touched on many of the areas where sustainability intersects with coatings, such as the elimination of materials of concern (including VOCs, PFAS, marine pollutants, and biocides); the efficient production and use of paint; the focus on the recyclability of both products and packaging, and efforts toward lowering one’s carbon footprint. Gilbert stressed that to lower VOC content, formulators must first understand ASTM D-6886—the analytical method used to measure VOC content and thereby determines what is considered a VOC—as well as monitor the VOC content of their raw materials. Accurate data on VOCs in raw materials are needed to ensure that formulating software can correctly calculate the levels of VOCs. Also, formulators need to educate their raw material suppliers and set limits for raw material VOCs early in the development cycle. Gilbert said that the strategy for removing PFAS from paint formulations is to work with raw material suppliers to remove fluorosurfactants and to evaluate alternative technologies to meet performance properties such as block resistance, substrate wetting, and dirt resistance.
On the topic of making paint more efficiently, Gilbert stressed that some companies in the industry are already frequently using a zero-waste batch process but that they probably don’t get enough credit for it. In this process, the water that typically results from rinsing mixing kettles at the end of a batch, which now contains some paint solids, is then used in the next batch, thus eliminating the generation of waste. The efficient use of paint includes designing formulations for good coverage and hiding, as well as for better interior and exterior durability to extend the lifetime of a paint. For example, the industry has improved hiding with the introduction of higher hiding color pigments and binders and pigments that contribute to the proper spacing of titanium dioxide in the dry film, both of which lead to improved opacity. In addition, the improved dispensing accuracy of point-of-sale tinting equipment has enabled the use of more concentrated colorants, facilitating higher volume solids and better hiding.
Regarding recyclability, Gilbert mentioned the PaintCare™ paint recycling program,1 through which consumers in 11 states and the District of Columbia can drop off old paints that are then recycled into new paint products. Gilbert explained how Behr has addressed the recyclability of paint cans by developing a new all-plastic can. Made of 100% recycled plastic, the can is also 100% recyclable after it has been emptied and any residual paint, once it has dried, has been peeled away from the interior of the container and then disposed.
In the presentation titled “Novel Functional Coatings and Inks Fabricated with Biobased Polymers,” Shan Jiang, Ph.D., of Iowa State University described the use of biobased polymers in functional coatings. Jiang presented research on a biobased nanocomposite formed with cellulose and zinc oxide nanoparticles for the blocking of UV light in transparent films and discussed efforts toward developing an ink based on biobased cellulose polymers and silver nanoparticles for possible use in printing electronic circuits for space applications.
While attempting to develop a transparent coating for food packaging using biobased materials that protects sensitive food from UV light, Jiang and his team evaluated the combination of biobased polymers, such as starch, cellulose, and their modified derivatives hydroxyethyl starch (HES) and hydroxyethyl cellulose (HEC), with zinc oxide (ZnO) nanoparticles, which are known to be good UV absorbers. Jiang found that the films based on HES and ZnO nanoparticles (0.8% by weight) provided only a slight improvement in lowering UV transmittance compared with a traditional food packaging film, polyethylene terephthalate (PET), that used the same level of ZnO. In an interesting result, however, he observed that a film based on HEC and 0.8% ZnO significantly lowered the amount of transmitted UV light to about 6%, while maintaining excellent visible light transmittance (73%) and transparency. This film was also much thinner compared with other technologies with similar performance.
Scanning electron microscopy (SEM) showed that the HEC-based films form a unique fractal network of ZnO nanoparticles, while the HES-based films show clustering of the nanoparticles. The more even distribution of the ZnO leads to better UV-blocking properties for the HEC-based films. Jiang explained that, although they have similar molecular structures, the differing cis- and trans-configurations of HES and HEC (Figure 1) lead to a difference in persistence length, resulting in a more linear conformation of the HEC polymer and a more coiled conformation of the HES polymer. The different conformations impact how the ZnO nanoparticles aggregate, and for HEC-based films, the result is less clustering than in the HES-based films.
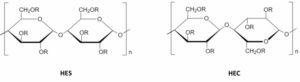
Figure 1. Molecular structure of hydroxyethyl starch (HES) and hydroxyethyl cellulose (HEC), with R being either H or CH2CH2OH.
Jiang also described the development of an ink based on HEC and silver nanoparticles, in which the HEC acts as both a stabilizer and viscosity modifier for the silver nanoparticles. The ink can be applied by electrohydrodynamic (EHD) printing, a process in which the ink is propelled to the substrate by an electric field. Using EHD printing, the ink can be applied in very high-resolution lines with a width of just a few microns on flexible substrates and in low gravity. After sintering, the printed pattern has high conductivity. The intended application is to enable the printing of electronic circuits in space. Jiang explained that he and his team evaluated the EHD printing tests’ feasibility by running them in zero-gravity during parabolic flights, with good results.
A presentation titled “Incorporation of Sustainability and Circular Economy Principles in Product Development” by Mike Jeffries of Covestro also addressed sustainability. In it, Jeffries discussed how circularity requires cooperation and joint solutions with companies working alongside partners up and down the value chain. Jeffries also stressed that sustainable raw materials are available to formulators. One of several examples he gave was biobased aniline, which is used to produce biobased methylene diphenyl diisocyanate (MDI). Based on the biomass of unrefined sugar from corn starch, wood, or straw, MDI is produced first through biocatalysis whereby the sugar becomes pre-aniline via use of microorganisms, and then with a second chemical reaction step whereby the pre-aniline material becomes 100% biobased aniline. The aniline is further reacted to eventually form biobased MDI.
Jeffries also stated that pentamethylene diisocyanate (PDI) is the first aliphatic isocyanate with significant bio-content (71% renewable carbon) and offers a non-petroleum alternative to isocyanates such as hexamethylene diisocyanate (HDI). In addition, he described how the biobased PDI compares favorably with HDI for performance when formulated into coatings. He then spoke about the joint solutions that are enabling Covestro to work toward biobased HDI. For example, Covestro worked with Genomatica to develop biobased hexamethylene diamine (HMDA), the precursor to HDI, using biotechnology and renewable plant-based feedstocks. According to Jeffries, these are just some of the examples of biobased raw materials that are becoming more available to coatings formulators.
Jeffries touched on how using coatings technologies that cure at lower temperatures can impact the use of energy in application. One example he gave is that using a two-component (2K) polyaspartic coating, which cures at ambient temperature, to replace a powder coating requiring an oven bake at 325 °F can result in a 75% reduction in energy usage at the manufacturing facility. Jeffries also discussed how the use of waterborne coatings can reduce both emissions and a company’s carbon footprint. For example, 2K waterborne polyurethanes that perform well enough can offer an alternative to solventborne 2K polyurethanes that rely on exempt solvents (e.g., Oxsol 100) to reach VOC targets.
Application Technology
Several very interesting presentations at the CoatingsTech Conference focused on new technologies for the coating application process. Brian Rearick and Ron Kralic of PPG gave a joint presentation titled “Precision Application Technology: Potential Benefits and Current Challenges,” describing a new coating application process that enables customization in two-tone automotive painting. Along with the trends of individualization and customization, two-tone color schemes for autos are becoming more popular. However, the traditional electrostatic spray process to paint a car in two colors is complex and labor and material intensive; it involves applying the first color (basecoat and clearcoat), curing, and then masking the car to enable application of the second color (basecoat and clearcoat) and another stage of curing. In the new process, the first color basecoat is applied, followed by precision application of the second color basecoat, and finally the clearcoat. Then the entire system cured. During this process, the second color coating is applied with precision jets onto the surface, resulting in very high transfer efficiency (>98%) and high edge resolution. The high resolution creates crisp lines, enabling printing of designs directly onto the surface in a maskless operation and with higher throughput.
In the presentation, Rearick described three emerging precision application methods. With air-actuated valvejet application, air triggers the valve, and the paint jets are either flowing continuously or turned off, which allows for a lot of area to be covered but with less detail. At the other extreme is piezo inkjet. Using many piezo heads, droplets are generated on demand, and the piezoelectric effect causes the heads to eject a drop onto the surface (drop-on-demand printing technique). This method has added complexity and is slower but provides very good resolution. Piezo inkjet also requires a paint that is more like an ink. In between the other two techniques is the piezo valvejet, which can be used to apply coating either continuously or on demand. It sacrifices some speed but provides good resolution. PPG is evaluating these techniques for their various business units, and Kralic described some of the challenges and the need to adjust formulations so that paint can be applied using these different application methods.
Some of the challenges of precision application include the requirement for lower viscosity coatings for use in microfluidic channels with high flow resistance and nozzle and filter limitations on pigment particle size and concentration. For example, the coating is applied through a very small jet orifice (~100 μm), and pigment particle size can have a big effect on stability under shear, agglomeration, and clogging. Kralic noted that pigments with particle size above ~5 to 7 μm tend to cause clogging, so limited colors are available right now (i.e., white, black, red, and blue), and effect pigments cannot be used. Substrate wetting and adhesion are also challenges, as are obtaining good jet stability, getting sharp edges to lines (high resolution), and obtaining the class A appearance required for automotive applications. As might be expected, properties such as rheology, solids content, and surface tension are important for controlling both droplet formation during application, substrate wetting, and sagging and appearance after application.
Also discussing the use of inkjet printing techniques for paint application but for aerospace applications, Kjersta Larson-Smith of Boeing gave a fascinating presentation titled “Inkjet Printing of Aerospace Decorative Liveries.” The current process used to repaint an airplane with new livery is a time- and labor-intensive process with a variable production rate that depends on the complexity of the livery design. After applying the body wrap color, the plane must be masked, the first livery color applied, followed by clearcoat application and touchup, and then the process is repeated for each successive livery color. A significant volume of masking material is used to achieve the final design.
Application of the decorative livery with inkjet printing, however, enables all colors of the livery to be applied at the same time, without masking between each color. Benefits include a reduction in production time of 2 to 12 days, a production rate which does not depend on the complexity of the livery design (i.e., each livery is applied in the same amount of time per area), and less waste of masking materials (e.g., tape, paper, stencils) because all livery colors are applied in a single process with no overspray. The use of automated robotics to apply the ink layer enables better safety due to less manual operations at heights. Less paint is wasted, solvents, and VOCs are reduced by 95%, and the standard livery color topcoats are replaced with a much thinner (0.1 mil) layer of ink, which results in a weight reduction of 60 to 150 lbs. for a typical Boeing 787 livery.
In the system, a white basecoat is applied first to give a blank canvas, and then the ink dots are applied for the colored livery. Because the colors used in some liveries lie outside the standard CMYK (cyan, magenta, yellow, and black) color space, a fifth color (orange) was added to expand the color set. A clearcoat is applied over the ink to improve durability. Larson-Smith acknowledged that inks do not always have the best durability but noted that the clearcoat appears to help with that potential problem. Accelerated weathering has shown good results, and panels are currently (as of the time of the presentation) on exterior exposure to generate natural weathering data. The presenter noted that the system meets all aerospace requirements.
Challenges include the requirement that the print heads remain very close to the surface (~ ¼ inch) throughout the application process, and the variation from plane to plane is more than that, so a method and sensors were developed to monitor the machine in real-time. Adhesion of the clearcoat to the ink layer was not always consistent, but use of an adhesion promoter solved that issue. Larson-Smith also explained that, due to crosslinking of the basecoat over time, the size of the ink dot applied at various times (i.e., basecoat age) can change (which can affect appearance), and therefore, the surface tension of the ink needs to be tuned to get good dot coverage. The presentation finished with a discussion of a real-world case study where the inkjet process was used to produce a photorealistic livery design on a vertical tailfin section of a Boeing 737, which has been in service for about 16 months. Although a full aircraft cannot yet be done in their facility, work continues developing this unique process.
A third presentation on application technology was titled “Real-Time, Accurate, Non-Contact In-Process Thickness Measurement of Paint, Automotive and Other Industrial Coatings,” presented jointly by Vivek Komaragiri of Sensory Analytics and Margaret Harrison of Sherwin-Williams. They detailed the SpecMetrix® technology, which enables thickness measurement of wet or dry coatings in real-time during a process such as coil coating. Komaragiri explained that state-of-the-art thickness measurement is typically done off-line, but that the new technology can be used during the process and is an optical method that gives absolute thickness measurement without the need for calibration.
The technology is based on proprietary ruggedized optical interference (ROI) technology, and according to Komaragiri, it addresses some key limitations of traditional optical interference-based measurement techniques. Figure 2 shows an illustration depicting the concept behind the ROI technology, where an electromagnetic wave is reflected from both the surface of the coating and the surface of the substrate. The reflected waves create an interference wave, and the frequency of the interference wave is directly proportional to the absolute thickness of the coating. Proprietary algorithms convert the interference wave pattern to a coating thickness. The method can be used on transparent films with 0.2 to 250 μm film thickness and pigmented films of 1 to 25 μm. A related technique extends measurement of transparent films from 0.75 to 350 μm and pigmented films from 0.75 to 75 μm. The technology also enables the simultaneous measurement of multiple coating layers (e.g., basecoat and clearcoat) because a reflection is generated from each interface of the multi-layer system.
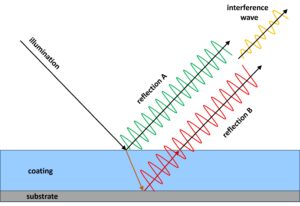
Figure 2. Illustration of the optical interference method, where an interference wave is generated from the interference of reflection A (from the coating surface) and reflection B (from the coating/substrate interface).
Harrison discussed the utility of the SpecMetrix system in the analysis of coil coatings, and explained that different coating technologies require their own set of SpecMetrix parameters based on how they interact with light. A validation process is used to determine the best set of parameters for a class of coatings and correlated with other measurement techniques to ensure accuracy. In a coating process such as a coil coating line, thickness measurements can be taken as the line is moving, with up to 150 measurements per second. This enables real-time analysis of whether a coating system is being applied within specifications.
Mattiello Lecture Award
In the Mattiello Lecture, Kurt Wood, who has more than 30 years of experience in the coatings industry, presented an excellent address titled “Visualizing How Coatings ‘Fail’–Service Life Viewed Through the Lenses of Coatings Science.” He discussed the weathering of coatings as the culmination of molecular events that have macro consequences. In other words, changes are caused by environmental factors such as temperature, water, light, or mechanical stress; occur on the molecular or nanoscale; and eventually result in observable macroscale changes such as film cracking or color change. He provided examples from his studies of PVDF (polyvinylidene fluoride) coatings of how weathering processes can be visualized by developing models of both the molecular scale and the macroscale changes.
For PVDF coatings, Wood described how chalking resistance is the key to its long-term durability and cited the contraction model of chalking and gloss loss developed by Colling and Dunderdale as helping to explain the excellent weatherability of PVDF.2 In the contraction model, mass loss occurs as polymer breaks down and erodes from the coating, leaving behind pigment particles. When the pigment volume concentration (PVC) at the surface is above the critical PVC (CPVC), pigment comes off the surface and chalking occurs. Applying that model to a blend of two miscible polymers with greatly differing erosion rates, such as found in the typical blend of PVDF and acrylic resins used in coatings based on Kynar® fluoropolymers, explains the excellent weatherability of those coatings. PVDF polymer is very resistant to photodegradation, and as long as there is enough PVDF in the film to keep the pigments encapsulated and bound together (i.e., PVC < CPVC), chalking and color fade will be minimal, even as the acrylic polymer degrades. By keeping PVDF at approximately 70% of the PVDF/acrylic blend, that condition is met, and the resulting durability is excellent.
Traditional PVDF-based coatings are solventborne baking systems typically containing about 70% PVDF and 30% of a compatible acrylic. The polymer blend achieves the required film morphology and polymer distribution required by this differential erosion model to result in low chalking and color fade. Wood described efforts in developing ambient-cure waterborne versions of PVDF/acrylic polymers (Kynar Aquatec®) and how resin distribution depends on the initial latex morphology (e.g., blend vs. core/shell vs. interpenetrating network). The waterborne versions have demonstrated weathering equivalent to the solventborne versions, with approximately 17 years of natural weathering data now available in addition to accelerated weathering.
Wood discussed how in the model of a photooxidation cycle, the rate of peroxide radical (·OOH) formation is proportional to the concentration of abstractable protons, which is proportional to the amount of acrylic in the resin blend. For that reason, color fade was found to be proportional to the percentage of acrylic in the blend. He also discussed how pigments—and in particular, organic pigments—can affect color retention in PVDF coatings. For example, it was noted that in many cases, the color retention of the waterborne systems is better compared with baked PVDF coatings. Wood suggested the differences may be due to changes in photochemical stability of the pigments caused by the high temperature baking cycles, perhaps from changes in the crystal structure. In addition to the summary mentioned above, Wood also provided other interesting and useful insights on the weathering of coatings.
Plenary Address
For the plenary address, Victoria Scarborough offered a presentation titled “A Heat Map of New Technology in a Post-Pandemic World.” In the address, Scarborough discussed six megatrends that are driving the development of technology and how they present opportunities for the coatings industry: global health, reshoring for economic stability, digitalization, global EV (electric vehicles), sustainability and resiliency, and climate change.
Speaking on the global health megatrend, Scarborough highlighted how the COVID-19 pandemic taught us how severe the repercussions of a global health problem can be. The world learned how to deal with supply chain disruptions, shipping delays, raw material price increases, loss of workers, and production issues compounded by extreme weather events, as well as with a rapid V-shaped recovery. Following the pandemic, part of the so-called “Big Reset” was dealing with the second trend Scarborough pointed out: reshoring for economic stability. Because of issues like supply chain instability, the failure of just-in-time manufacturing in the face of material shortages, and a lack of domestic supply, many industries are trying to build more resiliency in their supply chains. For the coatings market, this means formulating with alternate raw materials in mind and having multiple sources of supply.
Scarborough described the megatrend of digitalization as including artificial intelligence, machine learning, 3D printing, and robotics. An opportunity for coatings exists in 3D printing because parts are rough when manufactured, and coatings present an alternative method for smoothing the surfaces. The use of 3D printing in construction to make buildings from concrete is another opportunity that Scarborough highlighted. The application could cause a shift in the residential architectural paint sector, with more focus on coatings for cementitious substrates and properties such as alkali and water resistance. It could also drive the use of more expensive, high-performance coatings such as epoxies and polyurethanes.
Touching on the intersection of coatings and EVs, Scarborough noted the high growth in EVs does not necessarily increase the number of cars being sold but rather introduces new components that need coatings, such as battery packs and components of the electric drive system. The EV battery coatings market is currently $330 million and expected to grow to $1 billion in the next five years. Coatings are used for heat protection and to minimize the risk of fire and electrical interference. Scarborough concluded by addressing the megatrend of climate change, noting that because natural disasters are becoming more frequent and intense, the restoration and remediation market is expected to grow at an annual rate of nearly 6%. Bolstering this trend, she noted, homeowners have an increasing awareness of the health issues associated with mold and mildew creating a demand for effective solutions. The paint industry obviously has a role in restoration and remediation and can therefore take advantage of this trend. Other coatings needs that are driven by climate change include increased exterior durability, fire-resistance treatments, products to create tighter building envelopes, and thermal-management coatings such as cool-roof coatings. While discussing the growing opportunities for cool-roof and cool-wall coatings, Scarborough urged the audience not to forget the potential and opportunity for the development of cool-pavement coatings.
Thermosetting Cure Technologies
Several presentations concerned industrial coatings and their crosslinking technologies. One such presentation, by Stephanie Vanslambrouck of EMCO-Inortech, was titled “Carbon-Michael Addition: Single vs. Dual Cure.” The study involved reacting a malonate with various acrylates in both single- and dual-cure systems. In the single cure system, the malonate (a Michael donor) was reacted with the acrylate (a Michael acceptor) in a Carbon-Michael reaction catalyzed by a strong blocked base (Figure 3). In the dual-cure system, excess acrylate and a photoinitiator were incorporated into the formulation, and after the Carbon-Michael reaction, they were allowed to proceed for a certain amount of time (induction time), and then the remaining acrylate was crosslinked under UV light. The ultimate goal of the research is to create densified wood by impregnating natural wood with the system and curing to generate wood with higher hardness.
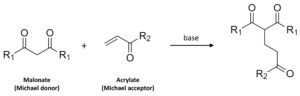
Figure 3. Carbon-Michael reaction catalyzed by a strong base.
Acrylates with either two or six unsaturated groups were investigated, as was a mixture of the two. For the dual-cure system, the acrylate:malonate stoichiometry was varied from 1.2 to 1.5, with the expectation that the excess acrylate would be available for the second reaction: photo-polymerization under UV light. Higher polymer glass transition temperatures (Tg) and crosslink density were obtained in the dual-cure systems, with shorter induction times leading to both higher Tg and crosslink density. In addition, for the same conditions of induction time and stoichiometry, the hexacrylate gives higher hardness and Tg than a mixture of di- and hexacrylate. Dual cure also improves the film hardness, but it appears that the induction time also affects the hardness, with shorter induction times leading to softer films. Vanslambrouk reported that their investigations continue, and that they have observed improvements in the hardness of wood by approximately 40% using a dual-cure system.
Kevin Turley of BASF discussed a new ultra-low temperature bake system that can help automotive OEMs meet key sustainability and carbon neutrality targets in a presentation titled “Ultra-Low Bake Coatings for Automotive OEMs.” According to Turley, global auto manufacturers have proposed ambitious carbon emission targets for themselves and their suppliers, with carbon neutrality being the ultimate goal. Studies have suggested that 50 to 70% of energy costs come from paint shop operations, and that 20% of the energy consumption is due to ovens used in the topcoat process. He explained how the existing 3-Coat-1-Bake (3C1B) process, which includes application of an adhesion promoter/primer, basecoat, and clearcoat, uses a final 20-minute bake at either 140 °C for metallic parts (car body) or 80 °C for plastic parts (bumper). Lowering the temperature of the topcoat bake could significantly lower energy consumption for the paint shop and have other advantages, such as enabling the baking of thermally sensitive plastics with the main body at the same time and potentially simplifying the paint lines used by auto manufacturers.
To that goal, Turley introduced a new ultra-low temperature bake topcoat system that cures at 50 °C. The new technology provides a 3C1B system that can both reduce carbon emissions and provide a Class A appearance over carbon-fiber reinforced plastics (CFRP), a substrate that is challenging to coat because of the difficulty in producing good aesthetics without multiple coating/sanding steps. Turley explained that the use of lightweight materials such as plastics and composites is expected to increase in the future and will be a key enabler of low bake systems.
The ultra-low bake system consists of a new 2K primer, a standard solventborne basecoat, and a new 2K clearcoat. Turley explained that the new system relies on the migration of isocyanate from the primer and clearcoat to assist in curing the basecoat. The system achieves Class A appearance over CFRP, as well as other bumper and body materials like thermoplastic polyolefins (TPO) and e-coated steel. In addition, testing shows that the new system is equivalent to a commercial bumper system (80 °C bake) for all target specifications (e.g., adhesion, thermal shock, imprint, weatherometer (WOM) exposure testing, etc.).
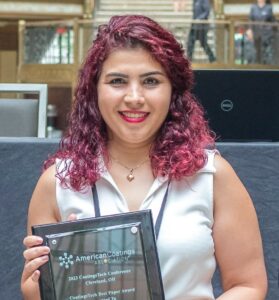
Photo Credit: Elaine Manusakis
Another presentation dealing with crosslinking technology titled “Thermally, UV, and Moisture Curable Novel Family of Versatile Oligomers” was by Tahereh (Neda) Hayeri, a Ph.D. candidate from Eastern Michigan University. Hayeri and co-author Vijay Mannari, Ph.D., who is a professor of polymers and coatings at the same university, received the CoatingsTech Best Paper Award, which recognizes the best overall paper that was submitted to the CoatingsTech Conference, and comes with a cash prize. Hayeri described a new high solids (100%), multifunctional oligomer that reacts via sol-gel chemistry. Sol-gel crosslinking reactions of an alkoxy-functional organosilane precursor can be catalyzed by using either strong acid or strong base catalysts to form an organic-inorganic hybrid network linked together by Si-O-Si bonds (Figure 4). A unique aspect of the new system is the use of blocked catalysts, which enable the crosslinking reaction to be triggered by either moisture, heat, or UV light.
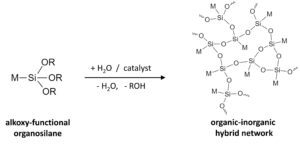
Figure 4. The catalyzed sol-gel reaction of an alkoxy-functional organosilane to form an organic-inorganic hybrid network (M = alkyl, aryl, or organo-functional group).
The oligomeric organosilane precursor for the sol-gel reaction was formed by the reaction of an isocyanate-functional precursor with an alkoxy-functional aminosilane. The organosilane precursor was then combined with the appropriate catalyst for the reaction conditions being investigated and a reactive diluent, tetraethyl orthosilicate (Si(OEt)4). A super acid photoinitiator catalyst was used for UV curing, and a quaternary ammonium blocked super acid catalyst (antimony-free) was used for thermal cure. For ambient temperature moisture cure, a tin-free super base catalyst was used. A combination of the photointiator and ambient catalyst was also evaluated for a dual-cure system, where UV curing was followed by ambient moisture cure.
Hayeri described how all four catalyst systems can trigger the sol-gel reaction and shared details of cure studies using both Fourier Transform Infrared Spectroscopy (FT-IR) and gravimetric techniques, showing good conversion and a strong effect of cure conditions on extent of cure. In addition, Hayeri also described the results of performance testing such as hardness, gloss, and methyl ethyl ketone (MEK) double rub resistance; efforts to produce a biobased version of the organosilane precursor, as well as ongoing studies to investigate the use of reactive diluents to assist in application properties and cure. More details of this exciting work can be found in the full paper, which is included in this issue of CoatingsTech.
References
- Information on the PaintCare™ program can be found at paintcare.org.
- Colling, J.H.; Dunderdale, J., “The durability of paint films containing titanium dioxide—Contraction, erosion and clear layer theories,” Org. Coat., 9(1), p. 47–84, 1981.
About the Author
Leo J. Procopio, Ph.D., is the president and owner of Paintology Coatings Research LLC. For more information, visit scienceofpaint.com or e-mail leo.procopio@scienceofpaint.com.