By Clifford K. Schoff, Schoff Associates
After a coating is applied, there is a period when the film is still liquid. Evaporation of solvent or water cools the surface and entry into an oven heats the surface. In either case, a combination of density and surface tension differences can cause convective flow within the film as shown in Figure 1. Material moves from the coating-substrate interface, rises to the surface, then drops back down. The motion continues until the coating has dried or cured enough to raise the viscosity to a level that stops flow. In multi-pigment systems, one of the pigments rising with the flow may be trapped at the surface producing the defects called flooding and floating. If that pigment completely covers the surface or has become the major component of the pigment mix at the surface, the result is a darker or lighter shade of uniform color. We usually call this flooding. Rubbing the wet paint with a finger (known as rub-up) will show that the surface color is different from the interior of the layer. Partial coverage by one pigment resulting in ugly streaks or mottled regions is called floating, although both defects sometimes are labeled as floating since, in both cases, pigment is floating to the surface. Flooding and floating both produce unacceptable color effects.
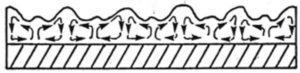
Figure 1—Diagram of convective flow showing the up and down pattern of motion.
Convective flow is readily observed by opening a can of aluminum pigmented paint. As solvent begins to evaporate, flakes will come to the surface and a network of cells will form. Similar cells occasionally are seen in coatings. These are called Bénard cells. They tend to be hexagonal in shape, but may be four- or five-sided or even roughly circular. Often, there is a mixture of forms as shown in Figure 2. Cells may be large (several cm across) or so small that a microscope is needed to see them. Networks of cells cause color irregularities in coatings with multiple pigments, including the highlighting of borders between cells. Pigment flocculation contributes to cell formation and flooding/floating because it encourages separation of pigments that are flocculated from those that are not, particularly if the latter has small particles that are more easily trapped at the surface.
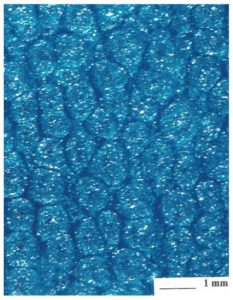
Figure 2—Example of a network of Bénard cells.
Bénard cells can produce surface effects such as roughness, low gloss, and waviness in virtually any coating, including clears. Cells in single pigment coatings have given matte appearance without the use of a matting agent (see Figure 3). It is rare for clears to show the hexagonal surface pattern, but there is some evidence that unexpected waviness in clearcoats and the waves induced in automotive basecoats by clearcoats in the early days of color plus cure development both have been due to convection flow.
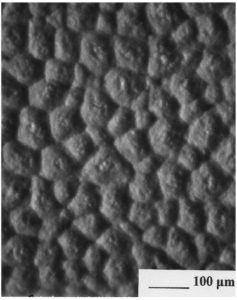
Figure 3—Bénard cells in a white can coating.
Convection flow can be prevented by lowering film thickness, increasing the viscosity of the coating, minimizing surface tension gradients across the film surface, and preventing or reducing flocculation. Thin multiple coats are less likely to suffer convection flow than a single thick paint film. Raising the viscosity will slow down the circulation pattern. Introducing a surfactant, low energy polymer, or oligomer that comes to the coating surface prevents surface tension gradients that arise from solvent evaporation and uneven heating. Reducing the rate of evaporation by reformulating with slower solvents has helped in some cases, but can make things worse if the coating dries too slowly. Flocculation can be prevented or reduced through better dispersion practices and the use of wetting agents. However, root causes of flocculation-related color problems can be complicated. I once worked on a problem with a medium blue maintenance paint that on spraying produced a light blue coating. A quick rub-up experiment showed that the color in the interior of the film was correct. We tried a wetting agent and several other additives, but whatever we did produced a color that was too light or too dark. The main pigments were phthalo blue and TiO2 and our actions always seemed to cause one of them to flocculate and allowed the other one to come to the surface. We eventually figured out that the solvent package for the resins was too good a solvent for the dispersing resin used for the pigments. On letdown, dispersing resin was stripped off the pigments, which interfered with dispersion quality and allowed flocculation to occur. Going to a different solvent package for the resins along with a better letdown procedure (slower paste addition, higher shear) solved the problem. The situation of dispersant being stripped from pigments by resin solvents may be not be unusual and may explain other flocculation and color problems.